CNC gesteuerte Plasmaschneidanlagen - Made in Germany
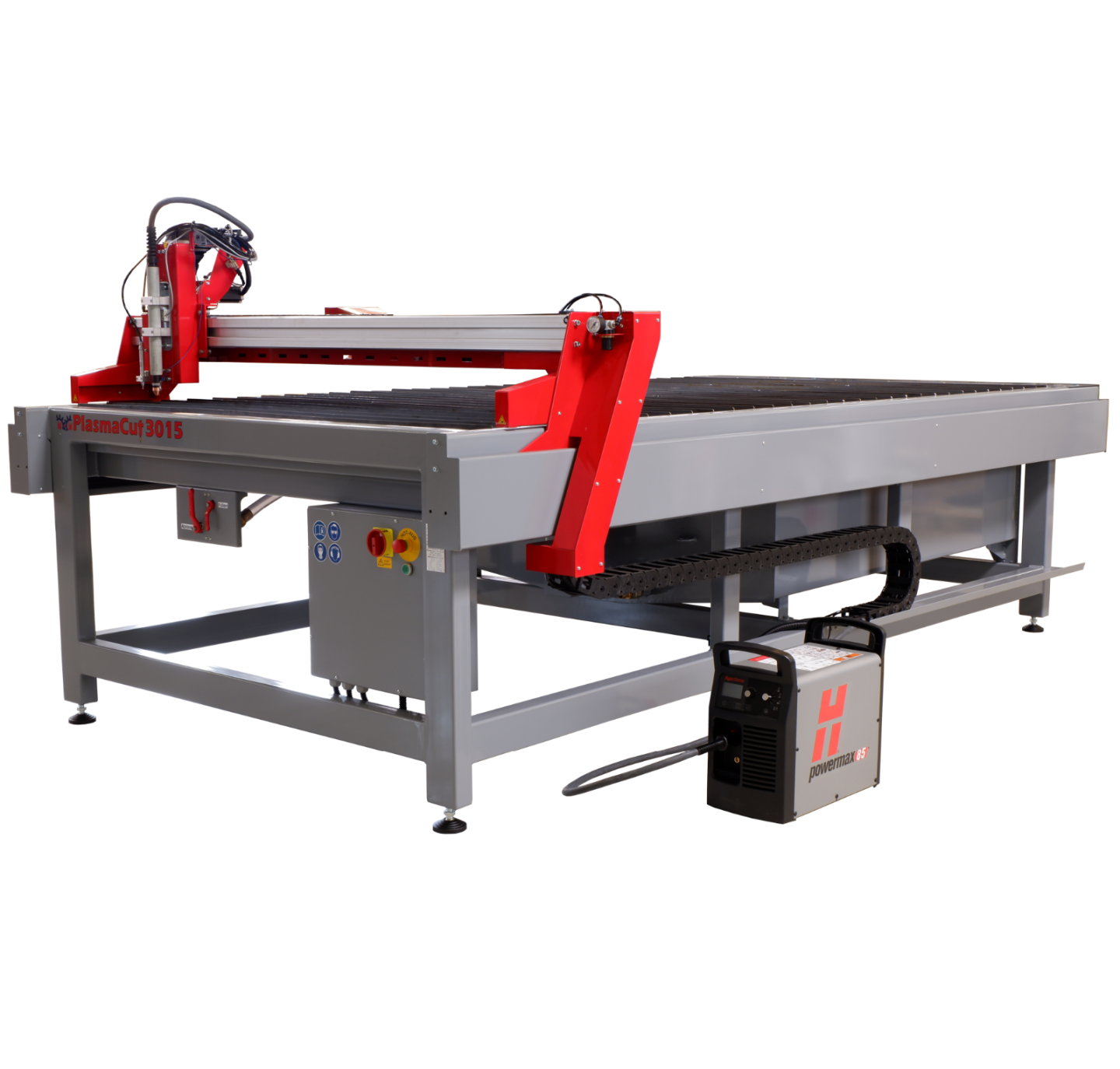
Varianten
- Die PlasmaCut ECO ist für kleine Betriebe geeignet in denen nicht jeden Tag Blechzuschnitte erfolgen müssen. Dieses System ist nur als Kleinformat 2000 x 1000mm erhältlich
- optional mit Wasserbett zur Reduzierung des entstandenen Schweißrauches
- THC (automatische Höhenregulierung) & Laserpositionierung inklusive
- mögliche Stromquellen: Hypertherm Powermax 45 XP bis Powermax 125
- Die PlasmaCut CNC ist für kleine wie große Betriebe geeignet. Hier sind vom Klein- über Mittel- bis hin zum Großformat alle Tischgrößen möglich. Diese Anlage ist für den ständigen Einsatz gebaut
- optional mit Wasserbett zur Reduzierung des entstandenen Schweißrauches und Vorbereitung für Zusatzabsaugung
- optional mit Anreißdorn und Gravierstift
- mögliche Stromquellen: Hypertherm Powermax 45 XP bis Powermax 125, Hypertherm MaxPro 200
- Die PlasmaCut PRO ist die Steigerung der CNC Variante. Hier wurde der Riemenantrieb, wie bei der CNC Variante verbaut, durch eine Zahnstange und closed loop Schrittmotoren ersetzt
- optional mit Wasserbett zur Reduzierung des entstandenen Schweißrauches und Vorbereitung für Zusatzabsaugung oder klappengesteuerter Absaugtisch
- optional mit Anreißdorn und Gravierstift
- mögliche Stromquellen: Hypertherm Powermax 45 XP bis Powermax 125, Hypertherm MaxPro 200, AutoCut, UltraCut, Smart Focus
Tischgrößen
Details | PlasmaCut 2010 | PlasmaCut 2512 | PlasmaCut 3015 |
Verfahrbereich | min. 2020x1020 mm | min. 2520x1270 mm | min. 3020x1520 mm |
Brückendurchlass | 120 mm | 120 mm | 120 mm |
Abmessungen LxBxH | 2560x1460x1700 mm | 3060x1760x1700 mm | 3560x1960x1700 mm |
Gewicht ohne Tank | 450 kg | 550 kg | 650 kg |
Gewicht mit Tank | 650 kg | 800 kg | 1000 kg |
max. Auflagegewicht | 400 kg/m² | 300 kg/m² | 250 kg/m² |
Volumen Wasserwanne | ca. 300 l | ca. 470 l | ca. 630 l |
Vorteile
Made in Germany
Qualität Made in Germany: Konstruktion, Software, Fertigung und Service: alles aus einem Haus.
Solide Stahlkonstruktion
Komplett verschweißte Rahmenkonstruktion: verwindungsarm, stabil, belastbar. Aufstellen, Anstecken, Losschneiden!
Hoher ROI
Durch den niedrigen Anschaffungspreis und geringe Betriebskosten machen sich unsere Anlagen schnell bezahlt!
Bewährter Antrieb
Ausgelegt für langen Einsatz: Linearschienen, Zahnriemen, Motoren. Großzügig dimensioniert für den Einsatz in rauer Umgebung.
Unabhängigkeit
Teile selbst schneiden und Zeit und Kosten sparen. Vom Zeichnen zum Teil in wenigen Minuten!
Steuerungssystem / Software
Einfache Bedienung, voller wichtigen Funktionen und ständig weiter verbessert. In unserer Software steckt das Know-How aus jahrelanger eigener Praxis.
Durch die kompakte Bauweise, die einfach zu erlernende Software und den günstigen Anschaffungspreis ist das System besonders für die Anforderungen kleinerer und mittlerer Unternehmen konzipiert. Bei der Entwicklung wurde Wert darauf gelegt, ein einfaches (im Sinne von einfach bedien-, wart- und reparierbar) System zu konstruieren, ohne größere Abstriche in punkto Genauigkeit, Leistungsfähigkeit, Bedienfreundlichkeit und Funktionsumfang in Kauf nehmen zu müssen.
Allgemeiner Aufbau
Die Anlage besteht aus einer soliden geschweißten Stahlkonstruktion. Diese trägt den Auflagetisch mit Wasserbett, das Führungssystem, die Antriebseinheiten, sowie alle Pneumatik- und Elektronikkomponenten.
- Die Träger, auf denen sich die Führungsschienen befinden, sind vom Auflagetisch entkoppelt. Somit hat eine Durchbiegung auf Grund des Auflagegewichts keinen Einfluß auf die Genauigkeit der Anlage.
- Alle Anlagenteile werden mit einer 2k-Industrielackierung (Grundierung und Decklack) versehen. Standardfarben sind RAL5046 (Telegrau 2) für den Rahmen und RAL3001 (Signalrot) für alle beweglichen Teile.
- Sonderfarben sind auf Anfrage möglich.
Alle Komponenten sind in einem Block zusammengefasst, es sind keine weiteren Montage- und Einrichtschritte bei der Inbetriebnahme erforderlich. Getreu dem Motto:
Aufstellen - Anstecken - Losschneiden!
- Der Auflagetisch ist so konzipiert, dass Material mit der maximalen schneidbaren Stärke auf die komplette Fläche aufgelegt werden kann.
- Der Auflagerost besteht aus einzeln erneuerbaren Elementen (Flachstahl), welche in einer leichten Wellenform in die Trägerbleche eingesteckt werden.
- Dadurch wird bei (häufig vorkommenden) achsparallelen Schnitten ein Schneiden entlang eines Steges weitestgehend vermieden.
- Der Rost selbst liegt in einem Wasserbett, so dass die beim Schneiden entstehenden Gase und Stäube zum Großteil gebunden werden.
- Wassertank zum schnellen Heben und Senken des Wassers (Option)
Optional ist ein Wassertank erhältlich, welcher fest in die Anlage integriert wird. Er ermöglicht es, das gesamte Wasser (oder natürlich nur ein Teil davon) sehr schnell abzulassen. Dadurch können Kleinteile, welche durch den Rost in das Wasserbecken fallen, leichter entnommen werden. Das Wiederauffüllen der Wanne erfolgt mit Hilfe von Druckluft ebenso schnell.
Höhenregelung
Die korrekte Schneidhöhe - also der Abstand zwischen Düse und Material - ist von entscheidender Bedeutung für ein gutes Schnittergebnis und die Standzeit der Verschleißteile.
Unsere Plasmaschneidanlagen bieten zwei Möglichkeiten der Abstandsregelung: Rein mechanisch über einen Gleitring oder elektronisch über die Lichtbogenspannung. Beides hat Vor- und Nachteile.
Gleitring
Die Z-Achse ist schwimmend gelagert, kann sich also nach oben hin einige cm frei bewegen und liegt mit ihrem Eigengewicht (federentlastet) auf. Über gehärtete Gleitschrauben (ähnlich Schlossschrauben) wird der erforderliche Abstand Blech-Düse eingestellt. Höhenunterschiede, z.B. durch thermischen Verzug, werden ausgegelichen, indem die Schraubenüber das Blech gleiten und so die komplette Z-Achse ausheben.
Vorteile
- sehr einfache Bedienung, kaum Fehlbedienung möglich
- keine Parametrierung erforderlich
- Brennerhöhe bleibt konstant, unabhängig von Material, Schneidstrom, Düse und Schnittgeschwindigkeit
- Brennerkörper ist bei Kollisionen geschützt
Nachteile
- Gleitschrauben können empfindliche Oberflächen (Alu, Edelstahl) zerkratzen
- Brennerhöhe wird nicht immer exakt eingehalten, da liegengebliebene Schlacketeile den Brenner ausheben können
- in manchen Fällen, z.B. beim Schneiden in U-Profilen, stört der Gleitring (hier bietet die Software aber z.B. das Schneiden ohne Gleitring)
- Gefahr des "Hängenbleibens" an sich hochstellendem Material ist größer
THC - elektronische Höhenregelung
Die Lichtbogenspannung ist u.A. abhängig von der Länge des Lichtbogens, also vom Abstand Düse-Blech. Eine elektronische Regelung (PI oder PID) führt die Z-Achse so nach, dass stets eine vorgegebene Lichtbogenspannung erreicht wird.
Damit eine THC in der rauen Praxis aber auch verwendbar ist, sind einige Bedingungen zu erfüllen. Zum einen muss die Mechanik der Z-Achse ausreichend dynamisch sein, d.h. Motor und Führung müssen schnelle Bewegungen ermöglichen. Die Regelung selbst muss auf Änderungen der Sollspannung schnell reagieren, um bei hohen Schnittgeschwindigkeiten im Dünnblech die Schneidhöhe zügig anpassen zu können. Andererseits darf die Regelung selbst nicht zum Schwingen neigen. Diese Anforderungen sind mit einfachsten Zwei-Punkt-Reglern (Brenner-Auf / Brenner-Ab), wie sie im Hobbybereich Verwendung finden, nicht realisierbar.
Ein weiterer wichtiger Punkt ist, dass die THC mit der übergeordneten Bahnsteuerung interagieren kann. Wenn die Schnittgeschwindigkeit absinkt, z.B. weil diese in engen Radien nicht erreicht werden kann, muss die Höhenregelung blockiert werden, da anderenfalls die Achse auf das Blech fahren würde. Dieser Effekt tritt ebenfalls beim Schnittende oder beim Einstechen auf, da hier die Lichtbogenspannung schlagartig ansteigt, was ein unzulässiges Nachregeln der Z-Achse zur Folge hätte.
Bei der Verwendung ist zudem ein Kollisionsschutz für den Brenner erforderlich, welcher die Anlage beim Berühren eines Hindernisses stoppt und den teuren Brennerkörper vor Beschädigung schützt. Die Schutzvorrichtung besitzt idealerweise eine Zentrierung, so dass der Brenner auch wieder korrekt angebracht werden kann, ohne ihn aufwendig neu ausrichten zu müssen.
Selbverständlich berücksichtigt unser Steuerungssystem diese (und einige weitere) Faktoren!
Vorteile
- Schneidhöhe wird sehr konstant gehalten, dadurch Erhöhung der Verschleißteil-Lebensdauer
- berührungslos, dadurch kein Beschädigen von empfindlichen Oberflächen
Nachteile
- Lichtbogenspannung ist von vielen Faktoren abhängig (Material, Rost, Stromstärke, Düse...), daher ist ein Einstellen und Erfahrung des Bedienpersonals notwendig
- Risiko der Fehlbedienung höher, da einige zusätzliche Parameter notwendig sind